RCC SPUN PIPES:
RCC Spun Pipes (Reinforced Cement Concrete Pipes) was invented by Walter Reginald Hume (an Australian inventor and industrialist) in the year 1910 and at first it was made through spinning/centrifugal process. So, RCC Spun pipes are also known as Hume Pipes. These pipes are mainly used for sewerage, drainage, culverts, irrigation water supply/ transportation, service line and other infrastructure projects. Now a day’s these pipes are also used for covering different types of cables to protect them from outside damages.
These pipes are classified as pressure and non-pressure pipe viz. Np1, Np2, Np3 & Np4 are non-pressure pipes and P1, P2 & P3 are pressure pipes. These pipes are used in specific conditions & projects. RCC Spun Pipe has impressive durability, sustainability, has a long lifespan, remain functional and effective for many years. So, the users of the pipes are not disturbed for any pipe replacement or infer-structure rehabilitation oftenly. These pipes require less maintenance cost and semi-skilled people can maintain these pipes.
These pipes are manufactured mainly by spinning process. At first iron cage are prepared as per size of the pipe then it is fitted in a mould case and after fitting the cage in the mould case it is placed in the moulding machine. During spinning, concrete is poured manually in the mould case and pipes are manufactured by centrifugal spinning process. After production it is kept under sunlight for drying. After 24 hours it is removed from the mould case and submerged in the curing tank for about 7 to 14 days. After curing, the pipes are for dispatch.
R.C.C Spun pipes & allies Products ranging from 150 mm dia to 2000 mm dia of different Classes (viz NP-1, NP-2, NP-3, NP-4, P-1, P-2, P-3 etc) of Collar Joint & Spigot & Socket Ended.
TECHNICAL DATA
R.C.C SPIGOT PIPES/ COLLAR JOINT (I.S 458/2021 LATEST REVISION) CLASS- NP2/ NP3/ NP4/ P1/ P2/ P3 ETC.
1. Reinforcement | : | MS/HB wire of SWG [I.S 432 ( part II) – 1982/ I.S 280-197811) (i) Longitudinal Steel – (ii) Spiral Steel – |
2. Coarse Aggregate | : | (Stone chips I.S 383-1970), Pakur quality, sieving through 20,12.5, 10, 4.75 & 2.38 Mm size Sieves. |
3. Fine Aggregate | : | (Sand I.S 383-1970), River Kangsabati, screening through sieves 4.75 & 2.36 mm 600 & 150 microns. |
4. Cement | : | (I.S 455 –1976, 269-1976) (450/M3) OPC & PPC cement. |
5. Water | : | Edible quantity from well (18 ltr/50 Kg of cement). |
6. Concrete/Mortar | : | M 35 grade according to I.S 458/2021 cube tests are carried out by the authorized agencies as per I.S 456. |
7. Curing | : | Cast pipes are dismoulded after 24 hours and then cured in water in vat at least for 15 days. Dates of manufacturing of pipes are marked on |
8. Rubber Ring | : | (I.S 5382-1967, 3400 I, II & X –1965 specified tests are carried out by the Authorised agencies (Not requires for Collar Joint Pipes). |
9. Test of finished pipes | : | Absorption Test- Dimension Check Straightness tests- At the factory using a straight bar. Hydrostatic tests- At the factory by using of “ pressure gauge” having been Calibrated by authorized Agency. Three Edge Bearing tests : At the factory by using of “ pressure gauge” having been Calibrated by authorized Agency. Permeability Test. |
10. Log Book | : | Log books are maintained, where day to day details of production is recorded. |
Manufacturing Process for Production of RCC Spun Pipes:
The entire production process is divided in eight parts. These are (a) binding of iron cages (b) moulding of cages (c) mixing of cement concrete (d) production of pipe (e) drying of pipes (f) Demoulding of pipes (g) finishing of pipes (h) curing of pipes.
Binding of Iron Cages: It is the first stage of production of pipes. M.S wire is used to make the iron cages which will be placed in the middle of the pipe.
Moulding of Cages: It is the second part of production. The wire cages are placed in the iron moulds and after fitting the mould with the iron cage is placed on the production machine for production.
Mixing of Cement Concrete: During fitting of moulds, mixing process of cement concrete is started. The main items of cement concrete are cement, sand and stone chips.
Production of Pipes: After mixing of cement concrete the production unit is started and the concrete mixing is thrown into the mould case slowly. After some time the mould case is filled with the cement concrete. Then the speed of the production unit is increased. After 15 to 20 minutes the concrete become hard and it take the shape of a pipe.
Drying of pipe: After production, the pipe inside the mould is left for 24 hours for drying.
Demoulding of Pipes: After drying of pipes, the next process is demoulding. By demoulding, pipes are bremoved from the mould case.
Finishing of Pipes: If required, a little finishing touch is given to the pipes at this stage.
Curing of Pipes: After finishing of pipes the pipes are merged into the water for curing. The curing period is minimum 7 to14 days. After curing the pipes are lifted from the curing vat and they are ready for dispatch.
Click to View Details of RCC Spun Pipes as per I.S 458/2021.
Product Gallery
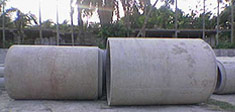
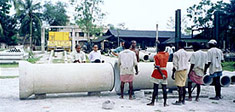
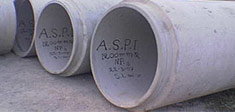